Last Updated on October 22, 2023 by Mark S. Taylor
To use a torque wrench, select the appropriate socket and set the desired torque value. Using a torque wrench ensures accurate tightening of fasteners.
It is a critical tool for maintaining the integrity of mechanical connections. Whether you are a professional mechanic or a diy enthusiast, learning how to properly use a torque wrench is essential. This versatile tool ensures that fasteners are tightened to the manufacturer’s specifications, preventing over-tightening or under-tightening, which can lead to mechanical failures.
We will provide a step-by-step guide on how to use a torque wrench effectively and ensure precise torque application for different applications.
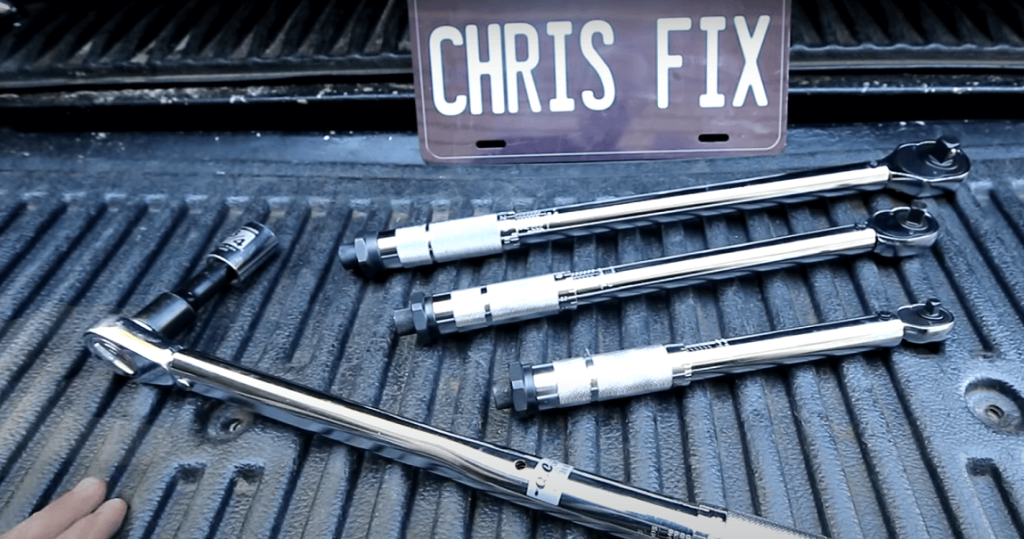
Contents [hide]
Why Mastering The Art Of Using A Torque Wrench Is Essential
Using a torque wrench may seem like a small and insignificant task, but it plays a crucial role in ensuring the proper functioning and longevity of your equipment and machinery. Whether you’re a professional mechanic or a diy enthusiast, understanding the importance of proper torque is essential.
Let’s explore why mastering the art of using a torque wrench is so crucial.
Importance Of Proper Torque
Proper torque is vital in many industries, including automotive, manufacturing, and construction. Here’s why it’s so important:
- Prevents loosening: Applying the correct amount of torque ensures that nuts, bolts, and other fasteners stay tight. This prevents potential hazards caused by parts coming loose during operation.
- Ensures optimal performance: Different components and materials have specific torque requirements. By using a torque wrench to apply the recommended torque, you optimize the performance of the equipment, ensuring it operates at its best.
- Maintains structural integrity: Over-tightening can lead to stress on the components, causing them to crack or break. On the other hand, under-tightening may result in loose connections, compromising the structural integrity of the machinery or equipment.
- Increases safety: Proper torque ensures that parts are securely fastened, reducing the risk of accidents or injuries caused by parts becoming detached.
- Avoids warranty issues: Many manufacturers specify torque requirements for their products. Failing to follow these guidelines may void the warranty. By using a torque wrench correctly, you can protect your investment and avoid any warranty issues.
Avoiding Under Or Over Tightening
Achieving the correct torque can be challenging, but it’s crucial to avoid under or over tightening. Here’s why:
- Under tightening: Insufficient torque can lead to bolts and nuts coming loose, resulting in the machinery or equipment malfunctioning. This can cause downtime, repairs, and potential safety risks.
- Over tightening: Excessive torque can result in damage to the threads, bolts, or other components. This can lead to costly repairs and the need for replacement parts. Additionally, over tightening can cause stress and deformation in the surrounding materials, compromising their integrity.
- Uniformity and consistency: A torque wrench provides a controlled and consistent force, ensuring uniformity in the application of torque across all fasteners. This helps to distribute stress evenly, preventing damage to the components.
- Precision and accuracy: Torque wrenches allow you to accurately apply the recommended torque, ensuring that each fastener is properly secured without exceeding the desired force. This precision helps prevent damage caused by applying excessive torque.
- Proper calibration: Regularly calibrating your torque wrench is crucial to ensure accurate readings. Properly calibrated torque wrenches provide reliable and consistent results, reducing the risk of under or over tightening.
Preventing Damage To Components
Using a torque wrench correctly is essential for preventing damage to components. Here’s why:
- Avoiding stripped threads: Over-tightening can strip the threads of bolts, nuts, or screw heads, rendering them unusable. This can result in costly replacements and delays in completing projects.
- Preserving gasket integrity: Proper torque prevents over-compression of gaskets, ensuring they maintain their integrity. This helps to prevent leaks and other issues that can arise from faulty gasket sealing.
- Reducing fatigue failure: Components subjected to excessive torque may experience fatigue failure over time. By using a torque wrench, you can apply the correct force, reducing the risk of fatigue failure and extending the lifespan of the components.
- Preventing material damage: Over or under tightening can cause damage to materials such as plastics, ceramics, or delicate surfaces. By using a torque wrench, you can apply the appropriate force without damaging the components.
Mastering the art of using a torque wrench is essential for maintaining the optimal performance, safety, and longevity of your equipment. Proper torque ensures that fasteners stay securely tightened, prevents damage to components, and avoids costly repairs. By understanding the importance of proper torque and following the recommended guidelines, you can confidently tackle any task that requires the use of a torque wrench.
Understanding Different Types Of Torque Wrenches
When it comes to using a torque wrench, it’s important to understand the different types available in order to choose the one that suits your needs. Each type of torque wrench has its own unique features and benefits. In this section, we will explore three popular types of torque wrenches: click-type torque wrenches, beam torque wrenches, and electronic torque wrenches.
Click-Type Torque Wrenches:
- Easy to use: Click-type torque wrenches are the most common and widely used type of torque wrench. They are designed with a click sound or a beep that indicates when the desired torque has been reached.
- Accuracy: These wrenches offer precise torque measurements, making them ideal for tasks where accuracy is crucial.
- Versatility: Click-type torque wrenches come in various sizes and torque ranges, allowing you to handle different applications effortlessly.
- Ratcheting mechanism: These wrenches feature a ratcheting mechanism that prevents over-tightening and ensures consistent torque application.
- Suitable for automotive and household applications: Click-type torque wrenches are commonly used in automotive repair and maintenance as well as for various household tasks.
Beam Torque Wrenches:
- Simple and reliable: Beam torque wrenches are known for their simplicity and reliability. They consist of a long lever arm with a calibrated scale and a pointer.
- Direct reading: The pointer on the scale directly indicates the torque being applied, offering accurate and consistent readings.
- Long-lasting: These wrenches have no internal moving parts, making them durable and require minimal maintenance.
- Ideal for heavy-duty applications: Beam torque wrenches are commonly used in industries such as construction, engineering, and aviation, where high torque values are required.
- Straightforward calibration: Calibrating a beam torque wrench is relatively simple, ensuring accurate readings over time.
Electronic Torque Wrenches:
- Precision and convenience: Electronic torque wrenches bring a new level of precision and convenience to torque applications. They feature a digital display that shows the applied torque in real-time.
- Programmable settings: These wrenches allow you to set specific torque values and provide audible or visual alerts when the desired torque is reached.
- Memory function: Electronic torque wrenches often have a memory function that stores frequently used torque settings, increasing efficiency in repetitive tasks.
- Data recording: Some electronic torque wrenches can record torque readings, enabling you to analyze and document torque values for quality control purposes.
- Suitable for professional use: Electronic torque wrenches are popular in professional settings such as manufacturing, aerospace, and machinery industries due to their accuracy and advanced features.
Understanding the different types of torque wrenches can help you select the right tool for your specific needs. Whether you opt for a click-type torque wrench, beam torque wrench, or electronic torque wrench, each type has its own advantages, ensuring precise and accurate torque application in various applications.
Select the torque wrench that aligns with your requirements and get ready to tackle any job with confidence.
Choosing The Right Torque Wrench For The Job
When it comes to using a torque wrench, selecting the right tool for the job is crucial. Considerations for different applications, factors to consider when selecting torque range, and assessing durability and quality are all important aspects to take into account.
Let’s dive into these key points:
Considerations For Different Applications
When choosing a torque wrench, it’s essential to consider the specific application you’ll be using it for. Different jobs require different levels of torque, so keep these factors in mind:
- Type of project: Whether you’re working on automotive repairs, home maintenance, or industrial projects, each application has unique torque requirements.
- Size and weight: Consider the weight and size of the wrench, as it should be comfortable to handle for extended periods.
- Accessibility: Some projects may have limited access or require working in tight spaces, so a compact or flexible torque wrench may be necessary.
Factors To Consider When Selecting Torque Range
The torque range of a wrench determines its versatility and suitability for a variety of tasks. Here are some important factors to consider when selecting the torque range:
- Project specifications: Check the manufacturer’s instructions or project specifications to identify the torque range required.
- Minimum and maximum torque: Ensure that the wrench you choose can cover the required torque range, including both the minimum and maximum levels.
- Adjustable or preset torque: Consider whether you need an adjustable torque wrench to handle multiple torque settings or a preset one for consistent torque application.
Assessing Durability And Quality
Durability and quality are crucial for a torque wrench, as it directly impacts its accuracy and lifespan. Here’s how to assess the durability and quality of a torque wrench:
- Materials and construction: Look for wrenches made from high-quality materials like hardened steel or alloy, ensuring they can withstand repeated use without losing accuracy.
- Calibration: Check if the torque wrench is factory calibrated and if it comes with a certificate of calibration to ensure accuracy.
- Brand reputation: Research different brands and read customer reviews to gauge the quality and reliability of their torque wrenches.
Remember, choosing the right torque wrench for the job is vital for accuracy, safety, and efficiency. By considering the specific application, torque range, and durability and quality of the wrench, you can ensure smooth operations and successful outcomes. So, take the time to evaluate these factors before making a decision.
Now that you have a better understanding of how to choose the right torque wrench, let’s move on to the next step: learning how to properly use this indispensable tool.
Getting Familiar With Torque Wrench Specifications
When it comes to using a torque wrench, understanding its specifications is crucial for achieving accurate and reliable results. Torque wrench specifications provide valuable information about the tool’s capabilities and limitations. In this section, we will explore the key aspects of torque measurements and units, decipher torque wrench specifications, and determine the appropriate torque range for different tasks.
Understanding Torque Measurements And Units
Torque is a measure of the turning force applied to an object, typically expressed in units of pound-feet (lb-ft) or newton-meters (nm). It is important to understand these measurements and units to ensure that the desired torque is applied correctly.
Here are some key points to consider:
- Torque measurements indicate the amount of force applied perpendicular to the length of a lever arm.
- Pound-feet (lb-ft) is the standard unit of torque measurement in the united states, while newton-meters (nm) is commonly used in other parts of the world.
- It is essential to use the appropriate units when referring to torque values to avoid confusion and ensure accurate torque application.
Deciphering Torque Wrench Specifications
Torque wrench specifications provide important details about the tool’s operating range and accuracy. These specifications help users determine the suitability of a torque wrench for a specific task. Here are some essential factors to consider when deciphering torque wrench specifications:
- Torque range: The torque range refers to the minimum and maximum torque values that a torque wrench can measure and apply. It is crucial to choose a torque wrench with a range suitable for your intended application.
- Accuracy: The accuracy of a torque wrench indicates how close the applied torque is to the desired value. Specifications usually state the percentage of the indicated torque in relation to the actual torque applied.
- Drive size: The drive size refers to the square-shaped socket on the torque wrench where various types of socket attachments can be used. Common drive sizes include 1/4″, 3/8″, 1/2″, and 3/4″, with each size suitable for different torque requirements.
- Length: Torque wrenches come in various lengths, which can affect the tool’s leverage and suitability for different applications. Longer wrenches provide greater leverage but may not be practical in confined spaces.
Identifying The Appropriate Torque Range For Your Task
To ensure proper torque application, it is essential to select a torque wrench with the appropriate torque range for your specific task. Here are some tips for identifying the correct torque range:
- Consider the manufacturer’s recommendations: Check the equipment or product manual for specified torque values or consult the manufacturer directly for guidelines on the appropriate torque range.
- Determine the material and size of fasteners: Different materials and sizes of fasteners require different torque values. Use torque charts or calculators to determine the appropriate range based on the specific fasteners being used.
- Consider the application: The torque requirements vary depending on the application. For example, automotive tasks may require torque ranges between 10-150 lb-ft, while industrial applications may require higher torque values.
By understanding torque measurements and units, deciphering torque wrench specifications, and identifying the appropriate torque range for your task, you can ensure accurate and safe torque application. Properly using a torque wrench enhances the quality and reliability of your work while preventing damage to equipment or fasteners.
Preparing The Torque Wrench Before Use
Before using a torque wrench, it is important to properly prepare and ensure its accuracy and functionality. Here are the key points to keep in mind when preparing the torque wrench:
- Checking calibration and accuracy: Before using the torque wrench, it is crucial to check its calibration and accuracy to ensure reliable and precise torque measurements. Here’s what you need to do:
- Make sure the torque wrench is set to zero or the lowest torque setting.
- Use a torque tester or calibration tool to verify the wrench’s accuracy.
- Apply a known torque to the tester and compare it with the wrench reading. If there is a significant discrepancy, the wrench may need calibration by a professional.
- Properly storing and maintaining the torque wrench: To prolong the life of your torque wrench and maintain its accuracy, proper storage and maintenance are essential. Consider these tips:
- Store the torque wrench in its protective case when not in use to prevent damage.
- Keep the wrench in a clean and dry area to avoid any corrosion or buildup.
- Regularly inspect the wrench for any signs of wear or damage, such as cracks or loose components.
- Clean the wrench after each use using a soft cloth to remove dirt and debris.
- Lubricate the moving parts of the wrench, as recommended by the manufacturer, to ensure smooth operation.
- Setting the desired torque value: Once your torque wrench is calibrated and adequately maintained, you can set the desired torque value based on your specific project requirements. Follow these steps:
- Determine the required torque specification for the fastener or component you are working with. Refer to the manufacturer’s guidelines or engineering specifications.
- Adjust the torque wrench to the desired torque value by rotating the handle or using the adjustment mechanism.
- Ensure that the torque settings are precise and match the required torque specification.
- Double-check the torque setting before applying force to avoid any errors or under/over tightening.
Remember, proper preparation of the torque wrench is crucial for accurate and efficient torque application. By following these steps, you can ensure reliable results and prevent any potential damage or complications during your projects. Now that you have your torque wrench ready, it’s time to put it to work with confidence.
Using A Torque Wrench Properly For Different Tasks
Step-By-Step Guide For Fasteners And Bolts
Using a torque wrench properly is crucial when working with fasteners and bolts. Here is a step-by-step guide to ensure accurate torque application:
- Select the appropriate torque wrench: Different tasks require different torque wrenches. Make sure you have the right one for the job.
- Prepare the fastener or bolt: Ensure that the threads are clean and lubricated. This will help with smooth tightening and prevent damage.
- Set the desired torque value: Refer to the manufacturer’s specifications or a torque chart to determine the correct torque value for your fastener or bolt.
- Attach the correct socket or bit: Use the appropriate socket or bit that matches the size and shape of your fastener or bolt.
- Apply torque gradually: Start slowly and increase the torque in small increments until you reach the desired value. Avoid applying excessive force all at once, as this can lead to over-tightening or stripping the threads.
- Pay attention to the torque wrench indicator: Most torque wrenches have a visual or audible indicator that signals when the desired torque has been reached. Stop applying force once you see or hear this signal.
- Check for any movement or give: After reaching the desired torque, check if the fastener or bolt moves or has any give. If it does, apply a bit more torque until it becomes stable.
- Release the torque: When you’re done, set the torque wrench to its lowest setting to release any tension on the internal mechanisms.
Applying Torque In A Controlled Manner:
Applying torque in a controlled manner is essential to prevent damage to fasteners, bolts, and other components. Here are some key points to keep in mind:
- Use a steady hand: Apply torque steadily and consistently without jerking or sudden movements.
- Avoid using extra tools or extensions: When using a torque wrench, refrain from using additional tools or extensions, as they can affect the torque measurement accuracy.
- Understand the torque wrench specifications: Familiarize yourself with the specific torque range and accuracy of your torque wrench. Using it within the specified limits ensures reliable and precise results.
- Regularly calibrate your torque wrench: To ensure accuracy, it’s important to regularly calibrate your torque wrench. Consult the manufacturer’s instructions for recommended calibration intervals.
- Watch out for torque variability: Be aware that different factors, such as temperature and thread lubrication, can affect torque variability. Take these factors into account to ensure precise torque application.
Methods For Ensuring Accurate Torque Application:
To ensure accurate torque application, consider the following methods:
- Double-check the torque specification: Confirm the correct torque specification for your fastener or bolt to avoid under or over-tightening.
- Perform a dry run: Before applying the final torque, perform a dry run to get a feel for the torque required. This can help avoid errors and ensure you’re applying the correct amount of force.
- Use a torque angle gauge: For certain applications, a torque angle gauge may be necessary. This gauge allows you to measure the degree of rotation applied to the fastener in addition to torque.
- Maintain a clean workspace: A clutter-free workspace reduces the chances of distractions or accidentally misapplying torque.
- Follow proper technique: Use the appropriate technique when applying torque, such as pulling directly in line with the wrench rather than at an angle. This helps maintain accuracy.
Remember, using a torque wrench properly for different tasks is essential for achieving accurate and reliable results. By following these steps, applying torque in a controlled manner, and utilizing proper methods, you’ll ensure successful and precise torque application.
Tips And Best Practices For Using A Torque Wrench
When it comes to using a torque wrench, there are certain tips and best practices that can help you achieve accurate and consistent torque application. Whether you are working in a cramped space or trying to avoid common mistakes, following these guidelines will ensure the effective use of your torque wrench.
Using A Torque Wrench In Cramped Spaces:
- Ensure proper positioning: In tight spaces, it can be challenging to position the torque wrench correctly. To overcome this, consider using extensions or adapters that can help you reach the desired fastener.
- Opt for a shorter handle: When working in cramped spaces, a torque wrench with a shorter handle can provide better maneuverability and ease of use.
- Angle attachments: In some cases, using angle attachments can help you reach areas that are difficult to access directly with a torque wrench.
Common Mistakes To Avoid:
- Over-tightening: One of the most common mistakes when using a torque wrench is applying too much force, leading to over-tightening. Always refer to the manufacturer’s specifications to determine the appropriate torque setting for the specific application.
- Using the wrong torque wrench: Different applications require different torque wrenches. Ensure you are using the correct type of torque wrench and that it is calibrated properly.
- Failure to reset: It is crucial to reset your torque wrench after each use. Failure to do so can result in inaccurate torque readings, compromising the integrity of your work.
Ensuring Consistent Torque Application:
- Lubricate fasteners: Applying lubrication to fasteners can help reduce friction and ensure consistent torque application. Be cautious not to over-lubricate, as it may affect the accuracy of the torque reading.
- Follow a sequential pattern: When tightening multiple fasteners, follow a sequential pattern instead of tightening them randomly. This approach helps distribute the torque evenly, reducing the risk of uneven pressure.
- Check for torque accuracy: Periodically, check the accuracy of your torque wrench by using a torque tester. This will ensure that the wrench is operating within the desired tolerance range.
By implementing these tips and best practices, you can use your torque wrench more effectively and achieve accurate and consistent torque application. Remember to always refer to the manufacturer’s guidelines and specifications for specific torque requirements in different applications.
Safety Precautions When Using A Torque Wrench
Using a torque wrench is an essential part of various mechanical tasks, ensuring that bolts and screws are tightened to the correct specification. However, it is crucial to prioritize safety when using this tool to prevent accidents or injuries. By following these safety precautions, you can ensure a safe and effective experience when using a torque wrench:
Wearing Appropriate Safety Gear
- Safety goggles: Protect your eyes from debris or metal shavings that may be generated during the tightening process.
- Work gloves: Provide hand protection and improve grip while handling the torque wrench.
- Ear protection: Reduce the risk of hearing damage in environments with loud noises.
Be Aware Of Potential Hazards
- Be cautious of pinch points: Avoid placing your fingers, hands, or any body parts in areas where they could get caught between the torque wrench and the object being tightened.
- Watch out for moving parts: Keep a safe distance from any moving parts of the torque wrench to prevent accidental contact and potential injuries.
- Be careful with the torque setting: Always double-check the torque setting before using the wrench to ensure it is appropriate for the specific task.
Proper Handling And Storage To Prevent Accidents
- Grip the torque wrench correctly: Hold the handle firmly and ensure a stable grip to maintain control throughout the operation.
- Store the torque wrench properly: When not in use, keep the wrench in a safe and secure location to prevent it from falling and causing injuries or damage.
- Inspect the torque wrench: Regularly check the wrench for any signs of wear, damage, or malfunction. If any issues are detected, have it repaired or replaced immediately.
By adhering to these safety precautions, you can minimize the risk of accidents or injuries when using a torque wrench. Always prioritize your safety and the safety of others around you. Stay cautious and attentive throughout the process to ensure a successful and secure outcome.
Troubleshooting Common Torque Wrench Issues
Identifying And Addressing Calibration Problems
If you’re facing issues with your torque wrench, calibration problems could be the culprit. Here are some key points to help you identify and address calibration issues:
- Pay attention to the click: When using a torque wrench, listen for a distinct clicking sound. If the click is too loud or too soft, it could indicate a calibration problem.
- Check the accuracy: Use a torque calibration tester to measure the accuracy of your torque wrench. If the readings are consistently off, it might require recalibration.
- Look for physical damage: Inspect your torque wrench for any signs of physical damage or wear. Bent handles or damaged internals can affect its calibration.
- Follow manufacturer guidelines: Refer to the manufacturer’s instructions for calibration procedures specific to your torque wrench model. They usually provide step-by-step guidelines for calibration.
Dealing With Malfunctioning Torque Wrenches
Sometimes, torque wrenches can experience malfunctions that go beyond calibration issues. Here’s what you can do if you encounter such problems:
- Clean and lubricate: Dust, debris, or lack of lubrication can cause a torque wrench to malfunction. Clean the wrench thoroughly, removing any dirt particles, and apply appropriate lubricant as per the manufacturer’s recommendations.
- Check for loose screws or bolts: Loose fasteners within the torque wrench can lead to internal malfunctions. Carefully inspect all screws and bolts, tightening them if necessary.
- Confirm proper storage: Improper storage can lead to damage and malfunctioning of torque wrenches. Store them in a protective case or wrap them in a clean cloth to prevent any potential damage.
- Avoid exceeding the limit: It’s crucial to stay within the torque wrench’s specified range. Exceeding the maximum limit can cause internal damage or trigger malfunctions.
Seeking Professional Help When Needed
In some cases, it’s best to seek professional assistance to resolve torque wrench issues. Here are a few circumstances where professional help may be necessary:
- Persistent calibration problems: If you’ve tried recalibrating multiple times but still face accuracy issues, it’s advisable to consult a professional calibration service.
- Internal component failures: If you suspect internal component failures, it’s best to have a professional technician inspect and repair your torque wrench.
- Warranty claims: If your torque wrench is under warranty and experiencing significant problems, contacting the manufacturer or authorized service centers can ensure proper repair or replacement.
By following these troubleshooting steps and seeking professional help when needed, you can ensure the accurate and efficient functioning of your torque wrench. Remember, regular maintenance and care are essential for prolonging the lifespan of your torque wrench and maintaining its accuracy.
Torque Wrench Maintenance And Care
Proper maintenance and care of your torque wrench are essential for ensuring its accuracy and longevity. By following a few simple steps, you can keep your torque wrench in optimal condition. Here are some key points to consider:
Cleaning And Lubricating The Torque Wrench
- Regularly clean your torque wrench to remove any dirt or debris that may have accumulated during use. This will help prevent contamination and maintain the accuracy of the tool.
- Use a non-abrasive cleaning solution and a soft cloth or brush to clean the surface of the torque wrench. Avoid using harsh chemicals that could damage the tool.
- Pay special attention to the moving parts, such as the ratchet mechanism and the adjustment knob. These areas tend to collect more dirt and may require additional cleaning.
- Once clean, apply a light coating of lubricant to the moving parts of the torque wrench. This will help reduce friction and ensure smooth operation.
- Use a lubricant specifically designed for torque wrenches, as using the wrong type of lubricant could affect the accuracy of the tool.
Testing For Accuracy
- Regularly test the accuracy of your torque wrench to ensure that it is still in proper working condition. This is especially important if you rely on the tool for critical applications.
- To test the accuracy, use a calibration tool or a torque tester that is specifically designed for torque wrenches. Follow the manufacturer’s instructions for the testing procedure.
- Apply a known amount of torque to the tester and compare the reading on the torque wrench with the desired torque value. If there is a significant difference, the wrench may need recalibration or repair.
- It is recommended to perform accuracy tests at regular intervals or whenever you suspect that the torque wrench may be experiencing issues.
When To Replace A Torque Wrench
- Over time, the components of a torque wrench can wear out or become damaged, resulting in decreased accuracy. Knowing when it’s time to replace your torque wrench is crucial for maintaining the quality of your work.
- The general rule of thumb is to replace a torque wrench every 5,000 to 10,000 cycles or every 12 months, whichever comes first. However, this may vary depending on the level of usage, manufacturer recommendations, and industry standards.
- If you notice any signs of excessive wear, such as slipping or inconsistent readings, it may be time to replace your torque wrench.
- Additionally, if the torque wrench fails the accuracy tests or cannot be calibrated back to the desired specifications, it should be replaced.
- Regular maintenance and care can extend the lifespan of your torque wrench, but it’s important to know when it’s no longer reliable for achieving accurate torque values.
By adhering to a regular maintenance routine, testing the accuracy periodically, and knowing when to replace your torque wrench, you can ensure that it remains a reliable tool in your arsenal. Keeping your torque wrench in top-notch condition allows you to achieve accurate and consistent results while avoiding costly errors.
Final Thoughts: Becoming A Torque Wrench Pro
So, you’ve learned the basics of using a torque wrench and successfully completed a few projects. Congratulations! But if you truly want to become a torque wrench pro, there are a few key points to keep in mind. Continuous learning and practice, developing a feel for proper torque, and embracing the importance of precision in mechanical work are all essential elements for mastering the art of using a torque wrench.
Continuous Learning And Practice
To excel in using a torque wrench, it’s crucial to adopt a mindset of continuous learning and practice. Here’s how you can achieve it:
- Stay updated: Keep up with the latest advancements and best practices in torque wrench techniques. Subscribe to industry newsletters, join online forums, and follow reputable sources to ensure you’re always in the know.
- Seek expert advice: Connect with experienced mechanics or professionals who specialize in torque wrench applications. Learning from their expertise can provide valuable insights and techniques to enhance your skills.
- Attend workshops or training sessions: If possible, enroll in workshops or training sessions specifically designed to improve your understanding and proficiency with torque wrenches. Hands-on experience and guidance from experts will help refine your technique.
- Practice, practice, practice: Regularly applying your skills with a torque wrench will not only reinforce your knowledge but also help you develop muscle memory. Seek out opportunities to work on different projects and experiment with various torque settings. The more you practice, the more confident and skilled you will become.
Developing A Feel For Proper Torque
Becoming proficient in using a torque wrench requires more than just manual dexterity. It involves developing a keen sense of feel for proper torque. Here are some tips to help you develop this skill:
- Start with a baseline: Begin by practicing with torque wrenches on standard projects where specific torque values are provided. This will help you establish a baseline understanding of what different levels of torque feel like in practice.
- Pay attention to feedback: As you apply torque, pay close attention to the feedback you receive from the wrench and the fastener. Notice the vibrations, clicks, or other indicators that signify reaching the desired torque level. This feedback will become invaluable as you progress in your journey to becoming a torque wrench pro.
- Experiment on different materials: Working with different materials will give you a broader perspective on the variations in torque requirements. Experimenting with various metals, plastics, or other materials will further refine your ability to gauge the appropriate torque for different applications.
- Trust your instincts: Over time, as you gain experience and practice more, you will develop an intuitive sense of when you have achieved the correct level of torque. Trust your instincts, but always verify with torque specifications to ensure accuracy.
Embracing The Importance Of Precision In Mechanical Work
In the realm of mechanical work, precision is paramount. To become a torque wrench pro, you must embrace the significance of precision in every project. Here’s how to ensure precision:
- Read and understand specifications: Before starting any project, thoroughly review the torque specifications provided by the manufacturer. Pay close attention to the recommended torque range, as exceeding it can lead to damage or failure.
- Use the appropriate torque wrench: There are different types of torque wrenches available for various applications. Ensure you’re using the correct type and size for the job to achieve the desired precision.
- Double-check torque settings: Before applying torque, always double-check your torque wrench settings. Mistakenly using the wrong torque setting can have serious consequences. Take the time to verify and avoid unnecessary errors.
- Maintain your tools: Regularly inspect and maintain your torque wrench to ensure its accuracy. Lubricate, calibrate, and store it properly to keep it in top condition. A well-maintained torque wrench will provide consistent and precise results.
- Record and document: Keep records of the torque values used for each project. This documentation will not only help you track your progress but also serve as a valuable reference for future endeavors.
Now armed with these final thoughts, you’re well on your way to becoming a torque wrench pro. Remember, continuous learning, developing a feel for proper torque, and embracing precision will be the driving forces behind your success. Practice, hone your skills, and let the torque wrench be your trusted tool in all your mechanical ventures.
Frequently Asked Questions For How To Use A Torque Wrench
How Do You Use A Torque Wrench Correctly?
To use a torque wrench correctly, first, set the desired torque value on the wrench. Then, apply the wrench to the fastener and tighten until the wrench clicks or signals the desired torque has been reached. Avoid using excessive force as it can lead to overtightening or damage.
Remember to consult the manufacturer’s guidelines for specific instructions.
What Are The Different Types Of Torque Wrenches?
There are several types of torque wrenches available, including click-type torque wrenches, beam-type torque wrenches, dial-type torque wrenches, and electronic torque wrenches. Each type has its own advantages, such as ease of use, accuracy, and versatility. Consider the specific requirements of your project before selecting the right torque wrench for the job.
What is the first step of using a torque wrench?
The first step in using a torque wrench is selecting the appropriate type and size for your specific task. Ensure it covers the required torque range and has the right features for your job.
What are three rules of torque wrenches?
Three important rules for using torque wrenches are:
- Always calibrate your torque wrench regularly to maintain accuracy.
- Store your torque wrench without tension to prolong its lifespan.
- Follow the manufacturer’s recommended torque values for your fasteners to prevent over-tightening or under-tightening.
How does a torque tool work?
A torque tool, like a torque wrench, works by applying a specific amount of rotational force (torque) to a fastener, such as a bolt or nut. It typically has a scale or display that shows the applied torque. Some torque wrenches have mechanisms that produce a distinctive “click” sound or a visual signal when the preset torque level is reached, indicating that you should stop applying force.
Conclusion
After reading this comprehensive guide on how to use a torque wrench, you should now feel confident in your ability to effectively and safely tighten bolts and nuts to the specified torque. Remember to start by selecting the appropriate torque wrench for your task, and always refer to the manufacturer’s instructions for specific settings.
When using a torque wrench, be sure to apply steady, even pressure and avoid overtightening. Regular maintenance and calibration of your torque wrench will also help ensure accurate results. By following these steps, you will not only prevent damage to your equipment and fasteners but also improve the overall safety and reliability of your work.
So go ahead and put your knowledge to use, and experience the satisfaction of precise and professional tightening with a torque wrench. Keep in mind that practice makes perfect, so keep honing your skills and always prioritize safety in all your torque wrench applications.